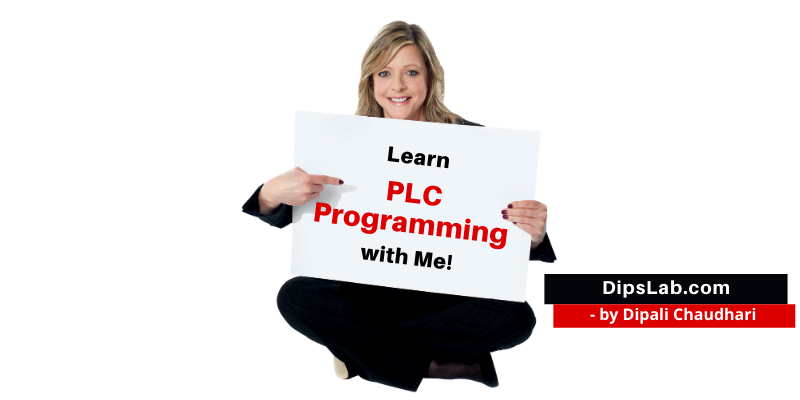
Are you here to learn more about PLC programming?
What is PLC? and why is it so important?
Programmable Logic Controller is a short abbreviation of PLC. PLC is known as ‘Primary Controller‘ or ‘Programmable Controller’.
In the enhancing mode and development of new technologies, the trend of PLC is evolving. It has become an integral part of the control system in an industrial environment.
What exactly is the Programmable Logic Controller [PLC]?
In this tutorial, I am describing the PLC in detail. Read this complete tutorial to learn PLC basics. I am explaining the working of PLC and its different types.
At the end of this article, you will find many of the day-to-day applications you can automate with PLC.
This is really interesting. Right?
Let’s start then…
What is the Programmable Logic Controller (PLC)?
Here is my simple and formal definition of PLC.
PLC is a solid-state control device or computerized industrial controller that performs discrete or sequential logic in the factory or automation environment.
If you get this definition completely or not, don’t worry. In this article, I will be explaining each of the terms mentioned this definition.
Basically, PLC is a combination of software and hardware. It acts as the brain of the machine or system for automation control systems.
Technical Definition of PLC:
The programmable logic controller is defined by ‘National Electrical Manufacture Associations [NEMA]’ as,
The digital electronic device that uses programmable memory to store instructions and implement specific function such as programming logic, sequence, timing, counting and arithmetic operations to control electronic machines and technical process.
This is how the Mini PLC looks like.
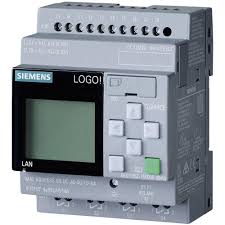
Schematic figure of the PLC (Compact PLC/ Mini PLC)
The PLC controller devices can be executed or operated by automatically and manually. For its operation, it consumes additional manpower, time, utility, and accurate operation in the system.
The most benefit of PLC:
It performs precise operations within very less time. And it consists of many components for controlling devices.
To understand the different operations performed by PLC, I am explaining each useful PLC component with the help of a block diagram in detail.
Basic Block Diagram of PLC System
The block diagram of PLC consists of different components. Each component has associated specific functions and operations in the PLC.
The list of basic components are.
- Input and Output Modules
- Power Supply
- Control Processing Unit (CPU)
- Memory System
- Communication Protocols
- Programming
You can see all these above PLC components in the below figure.
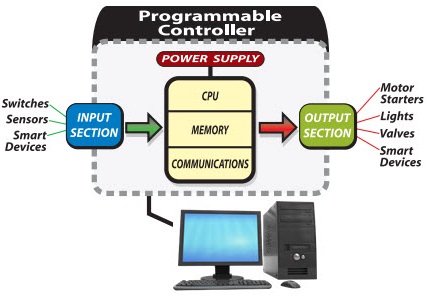
PLC System Image Source
Let’s see the description of the system one-by-one (PLC basics briefly explained).
1. Input and Output (I/O) Modules
The input/output modules in PLC are of two types. It can be either digital or analog.
Just like any other device or machine, we have to provide input to the PLC controller. It yields output.
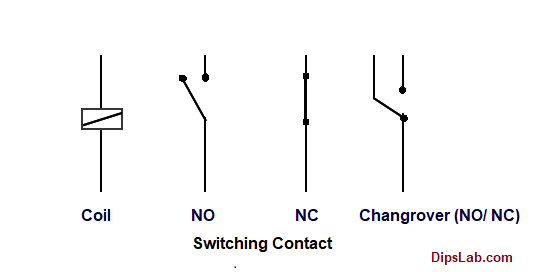
For example, when the user presses a button, the motor starts. Here the switch button is input. The motor is an output device.
In PLC, to take the input and to return the output, there are an I/O modules.
The input modules are used for providing an interface for input devices like different types of switches (push button switch, selector switch, limited switch), sensors, etc.
The output modules are used for providing an interface for output devices like motor, fan, relay, light, lamp, electric heater, solenoid valve, buzzer, etc.
You can learn PLC input and output modules in detail.
2. Power Supply
There is no science to make the electrical device works without providing a power supply.
Every device operates around you need power whether if its electrical or mechanical or any other power supply.
For PLC, we need an electrical power supply.
The power supply provides power to all other components to operates. It provides power to the input/output modules, memory system, and processor.
The function of the power supply is to provide the DC or AC power to operate the PLC.
How much power does it require to operate PLC?
Most of the PLCs work at 220VAC or 24VDC. You can learn the difference between AC and DC in detail.
3. Central Processing Unit (CPU)
Central Processing Unit is the heart of the PLC system. The function of the CPU is to store and run the PLC software programs.
It helps to perform the basic arithmetic, logic, controlling, and input/output operations specified by the instructions. It consists of the three subparts as memory, processor and power supply.
4. Memory System
A memory system is responsible for storing and retrieving data and information. It consist of different type of memory such as RAM, ROM, EEPROM and Flash memory.
Overall memory is classified into four sections based on the types of data it stores.
- Input/Output Image Memory
- Data Memory
- User Memory
- Executive Memory
5. Communication Protocols
The communication protocols are useful for exchanging the information or data between connected devices through a network.
For further detail, kindly check topmost 10 communication protocols used in PLC.
6. PLC Programming
You need PLC programming instructions and programming to live the communication between different circuits of the PLC.
The useful information or data are communicated by the specific communication protocols.
Most of the PLC programmer works on the ladder diagram programming language. It is pretty easy as compared to other PLC programming languages.
How does Programmable Logic Controller Work?
The most important working principle is- the PLC is operated by continuously scanning programs. Scanning happens every time per millisecond. So, it is called as the Scan Cycle.
For this scan cycle, PLC required a little amount of time in the range of milliseconds or ms.
What are the basic PLC Scan Cycle?
The scan cycle consists of the following three basic main steps.
- Read the inputs
- Execute the program by the CPU
- Update the output
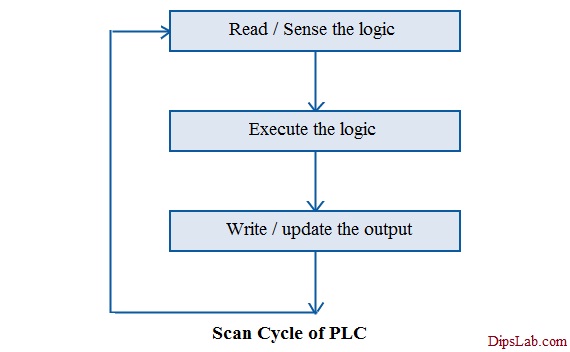
Step 1: Read / Sense the input
Firstly, PLC reads the on/off status of the external input signals. After scanning the input, it gets stored in the input memory. This input included switches, pushbuttons, proximity sensors, limit switches, pressure switches, etc.
Step 2: Execute the logic by the processor
This scanned input gets transferred to the CPU for processing from input memory. The processor executes the programming instructions based on the input. After the execution, the result (on/off) will be stored in the device memory.
Step 3: Update / write the output:
When the program executes the last instruction, it will send the on/off status to the output device memory. The outputs include solenoids, valves, motors, actuators, and pumps.
All three steps get completed under the scan time.
What is Scan Time?
The amount of time is taken by the processor to read/sense the first input and execute the last output called the Scan time.
PLC is so fast as it can easily scan and execute the program in few milliseconds i.e. 10-15 milliseconds.
What are the Types of Programmable Logic Controller (PLC)?
Two types of PLCs are used for commercial or industrial purposes.
- Compact PLC
- Modular PLC
Knowing these two types is the part of PLC basics knowledge.
What is a Compact PLC?
It is also called as Integrated PLC or Fixed PLC.
The compact PLC has a fixed number of input/output modules along with power supply and CPU.
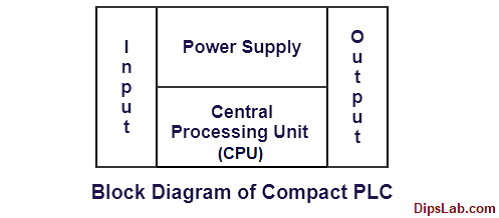
What is a Modular PLC?
It consists of a variable number of inputs and outputs. Inputs and outputs can be added to the modular PLC systems by the user.
If you look at the below PLC designing structure, it looks more like a rack. So, it is also called as Rack-Mounted PLC.
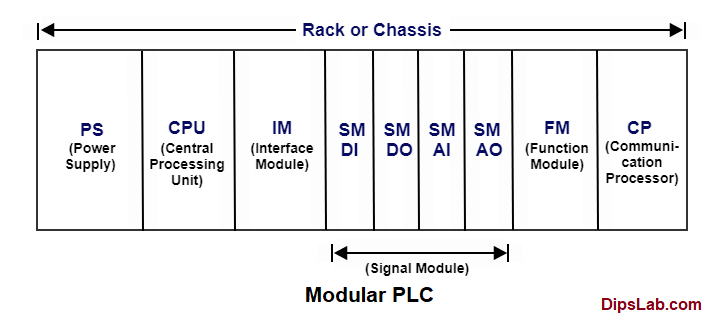
I have explained both compact and Modular PLCs in detail. Check the difference between modular and compact PLC.
What are the Most Popular PLC Programming Languages?
Based on the International Electrotechnical Commission(IEC) standard, PLC programming languages are classified into five main standards.
- Ladder diagram (LD)
- Instruction List (IL)
- Structured Text (ST)
- Function Block Diagram (FBD)
- Sequential Function Charts (SFC)
These are the topmost 5 different type of PLC programming languages.
According to the study and operations, ladder diagram (LD) is the widely PLC language for writing easily understandable programming logic. This programming logic based on the logic gates.
LD has a graphical user interface. It comes with many features that give an edge over other programming languages.
What is the most popular PLC brand used?
In the automation environment, more companies are manufacturing and working on the control system by using PLC and SCADA.
Today, there are multiple brands available for PLC systems. The Asea Brown Boveri (ABB), Allen Bradley (AB), General Electric (GE), Siemens, Delta, Mitsubishi, Omron, and Schneider are some of the very popular PLC brands.
Based on the usage, Siemens PLC tops the position. Allen Bradley PLC is at the second position in Automation.
You can use any brand of PLC as per your project requirements, study, and industry need.
What are the Applications of PLC?
For automation, multiple PLCs are used to monitor and control building systems in production processes.
PLCs are used in various industries like the steel industry, glass industry, cement industry, paper mill, coal mine, automobile industry, chemical industry, textile industry, robotic system, and food processing system.
In this PLC basics, I have already listed popular applications of PLC in industrial automation companies.
What are the Advantages and Disadvantages of PLC?
In an earlier article, I have explained the top 25 advantages and disadvantages of PLC over the relay system.
Learn more about PLC vs Relay system
This is all about the Programmable Logic Controller aka PLC. In this article, I tried to cover all the PLC basics required.
Some related PLC Articles:
- Industrial Automation Companies
- PLC Interview Questions and Answers
- PLC Based Automation Projects
- PLC Automation Training Institutes
If you have any queries, please hit your queries in the comment section. I will reply as soon as possible.
Happy PLC Programming!
Great!
Nicely compiled info.
Please write more details on specific applications
Thanks for your kind suggestion. I will be covering more about it in upcoming tutorials.
Thank you @Dipali Chaudhari for this great work. Please, I would like to keep updated with subsequent posts on this topic.
Thanks.
Sure, I will try to cover soon.
Thanks, you to reach out to my blog.
Thank you @Dipali Chaudhari for this great work. Please, I would like to keep updated with subsequent posts on this topic , its to much important topic in programme. If you
have more topic about electrical and electronic components so please make it also,
Thanks.
Thanks, Great information and very useful for basic plc knowledge.
Thanks, you too Sangam for reaching out to a blog 🙂
Great job
Thank you 🙂
Thanks. It’s really helpful for beginners like me.
You’re welcome! Glad you find it helpful.
Great write-up those who don’t know about PLC.
Very nice & good information.
Nitin Sonawane, Thanks!
Amazing stuff thank you
Thanks, Ishmael.
How to search for a job as a plc programmer Beginner?
Thanks, All information is very helpful.
Good
Thanks, Kamran Khan!
Thank you, mam, for sharing this useful information
You’re most welcome.
Very good
Thank you, Sunil Chawda:)
Interested to know more about Dipslab
Thank you, sir. I’m very much glad to see you here and your interest to know about DipsLab.
DipsLab.com is portal for Electrical and Electronics students where I share PLC- MATLAB Tutorials and my experience being an electrical engineer.
Please visit the website portal. It would be great receiving your feedback Sir for the betterment of the portal. 🙂
Nice information Madam
Thank you, Suraj Shete.
Interested
Thanks, SATYAM ROY
Thanks for sharing and giving the opportunity to learn
Harshit Jindal, Most welcome.
I am very much glad if my sharing knowledge can contribute to the learner.
Very helpful..
Thanks, Abin C M Panicker!
Seems like you have covered a half of the topics of an engineering subject PLC. Too useful contents and yes description too. Shared with the other’s students. Really thanks a lot for this mam.
Thank you, Rohan, for your kind words and sharing tutorials with students. I hope they enjoy it.
I will be covering the rest of the PLC tutorials soon.
Doing good…keep posting
Thank you, Jay Patel.
Very nice information.
Thanks, Pankaj 🙂
This tutorial is very nice for beginners like me. I will be reading more of your tutorials. Great work Dipali. Thanks!
Thank you so much, Mark. Glad to see you here and for finding my tutorials helpful.
Thanks for the wonderful tutorial.these is vary helpful for beginners like me.good doing well.
Most welcome, Kartik. Thanks for sharing your view of this tutorial.
Great article.
Thanks, Mark Saenz
Most valuable content….thanks for sharing.
Welcome, Hrishikesh! My pleasure to share knowledge for PLC learners.
Good question about PLC… fundamental question. Thank you
You’re most welcome, Rituraj.
Great! Can you also share some of the most common PLC programs used in the industry as well?
Lecture note well delivered and understood. Many thanks.
I am looking for PLC Tutorials and your great work on PLC is helping me a lot being a beginner.
Thank you very much, Hammad, for your feedback.
I am very cheerful when I saw my contribution helps others like you.
Very good Information thank you!!!
You’re most welcome, Govind.
Is it videos available?
Not at the moment. Soon, I will start my online video channel.
Good work. Keep it up.
Please, I need some more explanation on some advantages of PLC.
Thanks, for the compliment.
Kindly, what point do you want me clear? Please, elaborate.
Help me with a detailed pdf please.
Hie,
I am doing self-study on this topic. So, I have no kinds of stuff (book or pdf) related to PLC. You can refer my PLC tutorials. And you have any queries, you can ask me.
Thank you very much.
Now, I’m starting to learn PLC. Your blog is helpful to me.
Oh, that’s good. You are interested in learning PLC.
And thanks for sharing a few words for ‘DipsLab’. If you have any queries about the learning PLC, you can ask me. I will assist you.
Thanks, good job.
You’re most welcome!
Very helpful.
Also, I would like to know more about Ladder logic diagrams.
Hi Dipali Chaudhari,
Your website is very useful and presenting collective information for anyone who wants to basics of PLC /Electrical. Good on you, keep up the motivation and skills.
Much appreciated.
Thanks
Elayaraja Kaliyaperumal, CPEng
Thanks, Elayaraja Kaliyaperumal to reaching out to my blog.
I am very glad to hear such an inspirational word for the DipsLab. I am promising to you, I will try to do the best.
Glad, Yogesh 🙂
Thank you so much. This is very much helpful for me as a beginner. Thank you for the time you take out in writing this very helpful blog.
Thanks, you too Mansoor for reaching out to the DipsLab blog.
I am really glad, when I saw your inspirational words for the blog and my efforts.
I am promising that, I will share more technical tutorials for electrical and electronics engineers.
Really this article is very helpful for all beginners. Really tips you mention in programming is very helpful.
Thank you very much, Pankaj 🙂
Thank you so much, Mam. This article is very useful to me. And it gives some self-confidence
Oh, that’s great. Let’s go and build your skills and confidence.
If you have any queries, you can freely ask me. Surely, I will always assist you.
You are doing great job.I am interested.
Thanks, Mohit 🙂
Your site really inspires me a lot. There are many things to learn, so much information on it.
Thanks, Makxi, for shared inspiration words for the DipsLab blog.
Dear madam.
Excellent and great job! I would like to say a big thank you for sharing knowledge.
In this lock-down period, I just browsing the web in my leisure time and I came across your blog.
First of all, I would like to introduce myself about technical background and what made me to learn all about PLC.
I have zero knowledge in PLC and electronics, because I am a hardcore mechanical engineer working in Projects since last 7 Years.
My personal experience what it motivates me to know about PLCs is. In my project’s software, guys are coming and installing the program, though I have practical knowledge of machinery I couldn’t do commissioning of machinery with my team.
So I just pondered my self and thought of utilizing some time to know new subjects meanwhile I came across your blog through google images and it tooks me step by step procedures through your blog and even couldn’t realized that am sitting continuously in front of computer for 6 long Hours:) finally I finished each and every topic, leftover with Programming instructions, timers and basic LD program.
I hope in the other 2 hours I will finish off understanding the fundamentals of aforesaid topics.
Kudos to you!!
Keep going..
Thanks, Vikram! I really appreciate your interest in learning and embracing new things.
I’m so glad you find my PLC tutorials useful for your learning. You just made my day with your kind words. Please, if you have time, submit your feedback.
Thanks again, Vikram 🙂
Good.
Thanks, Raj:)
Excellent. Informative
Thanks 🙂
Very very important information is available in this tutorial. It starts with very basic information. It’s important for learner.
Thank you, Mam. Keep it up.
Thanks, you too Mahesh 🙂
The above information is very useful to me madam as I am fresher willing to explore my career in industrial Automation.
I request you to do on SCADA also if possible madam.
Thanks for the suggestion.
Soon, I will try to share more informative articles (related to the automation) on DipsLab blog.
That’s a very good and crispy introduction about PLC. Your teachings are incredible.
Thanks a lot, Ahsan for sharing the few words.
Dear Madam,
Thanks for sharing wonderful tutorial and giving this opportunity to learn. Mam please make tutorial on HMI, SCADA and VFD.
Thanks,for commenting. Sure, I will try to cover all these topics.
Make videos on schneider plc programing.
Thanks, Santhosh for suggesting. Soon, I will try to share and start my YouTube channel.
Ma’am, am second year electrical engineering student.i wish to join in ABB or seimems as electrical engineer( or core company).can you suggest a way to learn PLC for an job oriented way?
Hi, Sreekumar
If you want to start your work in the core or automation field, that’s a must know, all the basic concepts of electrical and electronics.
In industrial automation, PLC, SCADA, DCS HMI, VFD, IoT, and many more things are the fundamental topics covered in it. So, you should well learn all these topics that are widely used in the automation sector.
For getting more theoretical and practical knowledge, more institutes are providing industrial training. Check here, Top PLC/SCADA Automation Training Institutes.
hi madam I have 7 years experience in Electrical maintenance
in industry” I want to lean plc’ madam pls suggest me which
plc course better.
Sorry, I have no ideas about a specific PLC course.
Very helpful. Thank you, Mam.
Thanks, Kaushlesh for reaching out to the blog.
Thanks for sharing this tutorial mam.very helpful
Thanks for sharing this tutorial mam.very helpful
Glad, you find it helpful.
Hi Madam I am very interesting to learn about PLC because your explanation in the tutorial is the best one.
Hi Madam I am very glade to learn PLC System from you its been so lucky to get you on this program. Once again is my pleasure.
You’re most welcome.
Hi Dipali,
I really apricate your effort, thank you
Glad to read your feedback. Thanks, Ravi.
So thank you mam for providing this important information. This is very useful for me.
Glad to see your comment that it finds helpful.
I am very glade to learn PLC System from you its been so lucky to get you on this program.
Thank you, mam, for all these informations.
You’re welcome, Akash 🙂
Very useful information for students.
Thank you for giving us a learning platform.
Thanks, Dnyaneshwar. I’m so glad you find my PLC tutorials useful. You just made my day with your kind words.
Thanks for sharing knowledge. It really help me to understand how PLC works. Good Bless you Dear Dipali.
Thanks, Jorge.
how can i download siemens PLC Proggramming software for practice
It does not easily get at free of cost. If you want to learn perspective, you can try Delta PLC software which is freely available.
Thank you very much. the information was so helpful in understanding PLC.
Keep it up.
Thanks, Baguma 🙂
Great overview of PLC basics! The block diagram really helps in understanding the structure, and your explanations of the different types and their applications are super informative. I appreciate the balanced look at the advantages and disadvantages too. Looking forward to more posts like this!
Thank you so much! I’m glad you found the PLC basics and block diagram helpful. I really appreciate your feedback, and I’m excited to share more content like this in the future. Stay tuned for more posts on industrial automation and related topics!
Great overview of PLC basics! I found the breakdown of different types and applications really helpful. It’s interesting to see both the advantages and disadvantages highlighted. Looking forward to more posts on advanced applications!
Thank you so much for your kind words! I’m glad you found the overview helpful and informative.