Are you preparing for a PLC job? Do you want to test your PLC knowledge? Or do you want to learn more about PLC?
I am curating a list of PLC interview questions and answers based on my experience working in the PLC domain.
Whether if you are fresher or experienced, this list of interview questions will add value to your PLC knowledge.
Here you go.
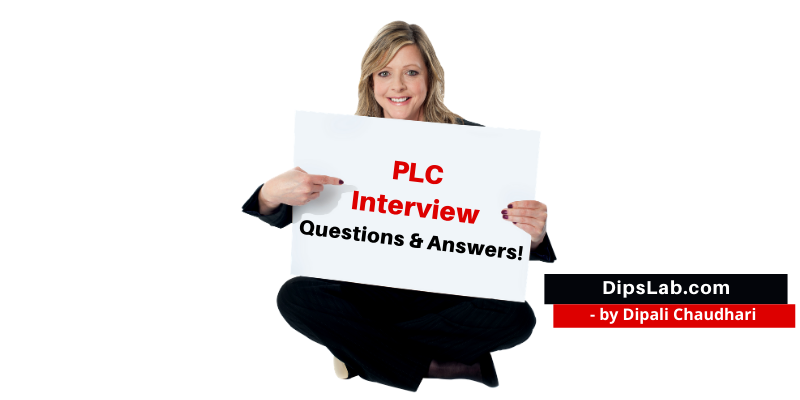
Important PLC Interview Questions with Answers
Go through each interview question. I have also explained the answer to each PLC programming question.
Question 1. What is PLC?
Answer: PLC is the short abbreviation of Programmable Logic Control.
PLC is a solid-state control device or computerized industrial controller that performs discrete or sequential logic in the automation industry.
PLC is a combination of software and hardware. It acts as the brain of the machine or system for automation control systems.
PLC is a digital electronic device that performs the following basic tasks.
- uses programmable memory to store instructions
- implement specific functions such as programming logic, sequence, timing, counting, and arithmetic operations
- control electronic machines and technical process
For more detail read more about PLC.
Question 2. Who is the father of PLC?
Answer: Dick Morley is called as the father of the programmable logic controller (PLC).
In 1968, under his study, he has created and developed the first industrial PLC i.e. Modicon PLC. The first Modicon PLC is built for General Motors.
Question 3. What is the role of PLC in Automation?
Answer: In automation, PLC is playing a significant role in controlling and monitoring industrial applications.
It has both hardware and software.
This controller device can be executed or operated by automatically and manually. For its operation, it consumes additional manpower, time, utility, and accurate operation in the system.
It is useful for increasing the reliability and stability of the system.
It performs precise operations within very less time. This is one of the reasons, today, PLC is widely used in the industry.
Question 4. What are the different components of PLC?
Answer: PLC has different components. Each component has associated with specific PLC operations and functions.
Here is the list of the useful basic components –
- Input and Output modules
These modules provide input to the PLC and yield output. Input and output can either be digital or analog types. - Power Supply
This component is responsible for providing AC or DC power supply to operate PLC. - Central Processing Unit (CPU)
CPU stores and execute PLC software programs. - Memory System
As the name depicts, the memory system is responsible for storing and retrieving information required for PLC operations. - Communication Protocol
There can be multiple devices connected to PLC. Communication protocols are used for exchanging information from one device to another. - PLC Programming (Software skill)
You need to write a programming language to implement PLC logic.
These are the six basic components of the PLC.
Question 5. What are the types of PLC?
Answer: There are two basic types of PLC based on the construction and working of PLC.
- Compact PLC
- Modular PLC
Questions 6. What are the different PLC brands?
Answer: The various companies are invented their own PLC brands. Here are some popular PLC brands.
- ABB PLC
- AB (Rockwell) PLC
- Siemens PLC
- Delta PLC
- Mitsubishi PLC
- Honeywell PLC
- Omron PLC
- Schneider PLC
- Hitachi PLC
- Fatek PLC
- Bosch PLC
- GE (General Electric) PLC
Siemens PLC and Allen-Bradley (AB) PLC are mostly used for project and educational purposes.
To know more detail about these PLC brands, follow this article.
Question 7. Explain the difference between Compact and Modular PLC?
Answer: This is the most important interview question for the fresher. I already explained the 9 differences between Compact and Modular PLC.
Question 7: What is the block diagram for Compact and Modular PLC?
Compact PLC block diagram:
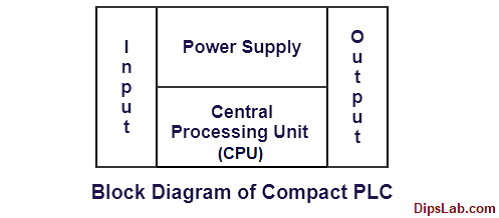
Modular PLC block diagram:
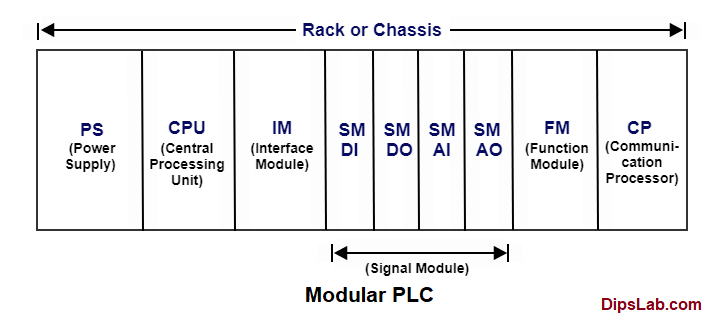
Question 8. What are the different programming languages used in PLC?
Answer: The programming language is used to create the program to control the PLC or automation system.
As per the IEC standard, five different types of programming languages are used in PLC.
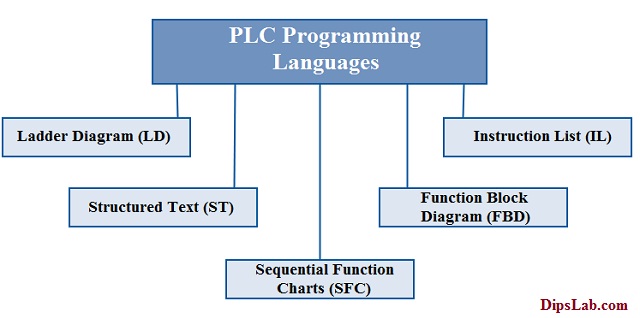
The list of different PLC languages used in the industry is as follows.
- Ladder Diagram (LD)
- Instruction List (IL)
- Structured Text (ST)
- Function Block Diagram (FBD
- Sequential Function Charts (SFC)
For more detail, learn five different PLC programming languages.
Question 9. What is LD in PLC?
Answer: LD is the short abbreviation of the “Ladder Diagram”. It is the most popular and universally accepted programming language for PLC.
It is easy to implement PLC logic with LD as it provides a graphical user interface.
LD is known as “Ladder Diagram Language” or “Ladder Logic Language”.
Question 10. What is rung?
Answer: In LD programming, the numbers of the horizontal lines are represented as the “rungs”.

Question 11. What is the timer?
Answer: Timer is the most essential instruction for PLC. The timer is used to operate and control devices for a specific duration of time. The programmer can set the timer based on the project requirement.
Question 12. What are the different types of PLC timers?
Answer: In general, there are three different types of timers used.
- On Delay Timer
- Off Delay Timer
- Retentive On Timer (RTO)
For practical, follow the tutorial to learn and implement PLC timer.
Question 13. What is the function of the RTO?
Answer: RTO is a Retentive On Timer. The main function of the RTO is used to hold or store the set (accumulated) time.
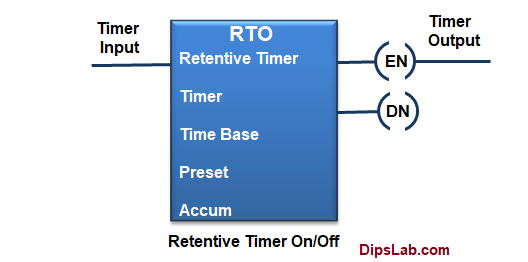
Question 14. What is the counter?
Answer: Counter is an instruction which is useful for sequential counting as digital numbers. It is part of the mathematical function.
Question 15. What are the different types of counters used in PLC?
Answer: The PLC counter is classified into three different types.
- Up Counter
- Down Counter
- Up/Down Counter
In PLC programming, the up/down counter is mostly used.
Question 16. What is the rack or chassis?
Answer: The modular PLC consists of a number of input or output modules, the controller processor, and the communication controller. This hardware assembly of these modules is called as “Rack or Chassis”.
Refer modular PLC block diagram mentioned in an earlier question.
Question 17. What is the PLC Scan Cycle?
Answer: When the PLC program is executed, there are multiple repetitive processes occurred. This is entire process is called a PLC scan cycle.
This scanning program consists of reading input data, executing the programming logic, and updating the output data in one cycle.
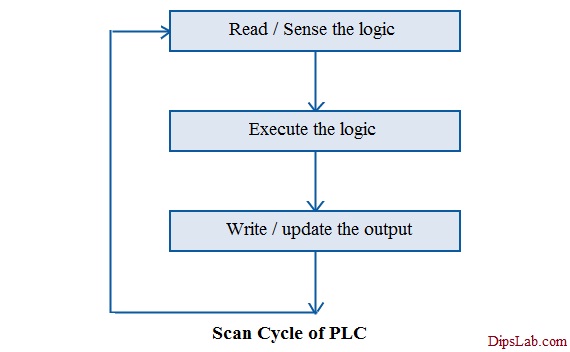
The scan time is the time required for continuously scanning programs. It takes approximately 10ms-15ms of time.
Question 18. What is the standard format for the digital I/O module address used in the AB PLC program?
Answer: The format for the digital I/O address is as below.
File type: Slot Number. Word Number/ Bit Number
This is the standard addressing format used in AB PLC’s brand.
Question 19. What is the MCR?
Answer: MCR is the short abbreviation of “Master Control Relay”. It is a type of instruction used in Siemens PLC software. This instruction is used to shut down the process.
There are some other types of MCR instruction like
- MCRA (Master Control Relay Active),
- MCRD (Master Control Relay Deactive),
- MCR< (Master Control Relay Less),
- MCR> (Master Control Relay Greater).
Question 20. What is Communication Protocol?
Answer: The system communicates with two or more communicating devices for transferring digital data or information. This communication is governed by some set of rules called as ‘Communication Protocol’.
The standard definition 0f communication protocol is a set of rules that govern data communication.
You can expect multiple PLC interview questions related to the communication protocol.
Question 21. What are the different types of communication protocols used in PLC?
Answer: In the PLC communication network, various types of protocols are used for communicating with multiple connected devices.
Here are some standard PLC communication protocols.
- EtherNet/IP
- Profibus
- Modbus
- Interbus
- ProfiNet
- ControlNet
- DeviceNet
- DirectNet
- CompoNet
- RAPIENet
- EtherCAT
- MelsecNet
- Optomux
- DF-1 Protocol
- HostLink Protocol
- MECHATROLINK
- DH- Data Highway
- PPI- Point to Point
- EtherNet Powerlink
- MPI- Multi-Point Interface
- EGD- Ethernet Global Data
- AS-i- Actuator Sensor Interface
- OSGP- Open Smart Grid Protocol
- DNP3- Distributed Network Protocol
- SDS- Smart Distributed System Protocol
- PieP- Process Image Exchange Protocol
- SRTP- Service Request Transport Protocol
- BSAP- Bristol Standard Asynchronous Protocol
- FINS- Factory Interface Network Service Protocol
- HART- Highway Addressable Remote Transducer Protocol
- Recommended Standard (RS-232, RS- 422, and RS-485) Protocol
These are the foremost communication protocols used for the PLC and other network connections. These protocols are supported by different PLC software brands.
The communication protocols are dependent upon three fundamental parts such as baud rate, network length, and the number of nodes. There are different functions associated with each protocol.
Question 22. Which types of sensors are used in automation?
Answer: The sensor is an electronic device that detects various parameters from the Physical environment and passes it as input to the PLC controller.
The sensor can be a digital as well as analog-type based on the type of signal it passes.
Here are various types of sensors used to communicate the different parameters to the controller.
- Inductive Proximity Sensors
- Capacitive proximity sensors
- Optical Sensors
- Ultrasonic Sensors
- RTD (Resistance Temperature Detectors) sensors
Question 23. What are the sinking and sourcing?
Answer: Sinking and Sourcing are very important concepts used for connecting a PLC correctly with the external environment. These two concepts are applied only for the DC modules.
The Sinking circuit provides a ground condition path to load (-DC ). And sourcing circuit provides a +24 v source to the load (+DC).
Question 24. What is the Redundant System?
Answer: The redundant system is a replica of the original system. When the original system breaks down redundant system takes charge of the original system and performs all the required operations.
It provides duplicate features of a running system. A redundant system is very useful when a failure occurs in the running system.
The following are the different types of redundancies.
- Input or Output (I/O) redundancy
- CPU redundancy
- Power Supply redundancy
- Communication protocols redundancy
- Bus system redundancy
The redundancy system is designed where Zerobreakdown is required.
Question 25. What are the advantages of the PLC over the Hardware Relay?
Answer: The following are the advantages of PLC over the hardware relay.
- PLC occurs in both software and hardware base. But relay occurs in only hardware base.
- PLC can easily monitor and control the device than the relay.
- It is easy to find out the fault in PLC software.
- PLC provides more working functions and features than the relay.
- PLC provides more flexibility and reliability than the relay.
- It is easy to modify and implement PLC programming logic than the relay.
Question 26. Explain the functions of PLC.
Answer: The functions of the PLC are,
- Sequential computerized controlling
- Monitoring the system and plant
- Operating the position or motion of the system
- Detecting the fault condition in the system
Question 27. What is the major area of applications of PLC?
Answer: PLC has multiple applications in various sectors.
- PLC is needful in the industrial sector like the steel industry, glass industry, cement industry, paper mill, coal mine, automobile industry, chemical industry, textile industry, robotic system, and food processing system.
- It is used in the electrical transmission and distribution power station.
- It is used for domestic purposes in remote sensing devices.
- PLC is also useful for educational purposes such as academic and research projects.
PLC is mostly used for commercial and educational purposes.
Question 28. What are the main advantages of PLC?
Answer: There are various advantages of PLC.
- PLC (especially Compact PLC) has a lower cost associated with it as compared to the other automation technology.
- It provides a more reliable solution.
- Even for beginners, programming used for PLC is easy to write and to understand, and to implement the logic. Among all PLC programming, LD language is the easiest one.
- One of the major advantages is, PLC is easy to communicate and connect with the computer. There are various standard communication protocols available in PLC.
- PLC (especially Compact PLC) does not take much space. They are smaller in size.
- PLC operates very fast (almost no booting time).
- Performing modification is possible and very much easy. You can easily make the changes in an already implemented design logic.
- PLC has low maintenance associated with it.
- PLC programming provides modularity. Modular design makes development easy.
- As we have seen earlier, PLC has a fast scan time (near about 10-15 milliseconds). It requires very less operation time to perform any task.
For these advantages, PLC is replacing hardware relay and it is industrially accepted.
Question 29. What are the disadvantages of PLC?
Answer: Apart from various advantages, there are a few disadvantages.
- With PLC, you can operate only one program at a time. You can not run multiple PLC programs simultaneously.
- There are some working environment limitations associated with PLC. The performance decreases in certain cases like high temperature, and vibration conditions.
Question 30. Explain the term downloading and uploading in PLC.
Answer: These two terms are related to the data transfer between PLC and connected PC.
- Uploading means data transfer from PLC to PC.
- Downloading means data transfer from PC to PLC.
Most of programmers get confused in these terms.
Conclusion:
These are the PLC interview questions and answers asked in many company interview rounds.
If you are looking for job opportunities in PLC, check out the list of electrical companies. Going through their official websites and career pages, you can find various job opportunities.
I hope this list of PLC interview questions will help you.
Feel free to post if you have any queries. You can also share your experience in attending job interviews. Hopefully, this will help many other job aspirants.
I have spent 3 days curating these interview questions. Please share this with your friends. Your feedback in the comment is highly appreciated.
Online PLC Quiz:
If you are ready for giving an online test quiz, here is a link of the online PLC Automation Quiz.
All the Best!
Greetings of the day,
I have seen something strange in the answer to question 30.
While I was taking the course of plc I saw that when we use the term upload the data from plc is transferred to pc and for downloading it transfers from pc to plc. Please correct me if I am wrong
Thanks for the corrections. You are right. Edited article! Please check.
You are right. But, in Siemens the question 30 is right.
UR CORRECT
You polished my brain, Ma’am
Please forward to such articles to my email ghorpadeshashank@gmail.com
Thanks,
From
SHASHANK GHORPADE
Hi SHASHANK,
Thanks for your feedback. Glad!
I will start writing a newsletter soon where I will share my writeups. Noted down your email.
Best wishes!
Shashank, kindly subscribes to my Newsletter. You will get an automatic update about my new tutorials through the mail.
Thank you very much Mam. It is very simple and easy to understand.
Thank you for sharing this with us. Because, it must had take some your time and energy.
Thanks, Milind. You made my day very special. I’m very glad that my effort and contribution becomes helpful to ‘DipsLab’ readers like you.
Good blog, useful for beginners to PLC Automation field.
However, point # 30 is not accurate. Siemens uses the reverse: Download to PLC and Upload to PG/PC. If my memory serves me right even AB & GE PLC’s use this terminology. It’s been a while since I worked on these two PLC’s, bit rusty but would all come back the moment I lay my hands on either of them.
Thanks, Rajesh for the correction. Edited article!
This is very interesting thank you very much if could you be able to send it to me via email
Hi, soon I will start sending the newsletter with my articles. Kindly share your email.
Kindly subscribe to my Newsletter, you will get an automatic update about my new tutorials through the mail.
Nice Maam
Thanks, Anand 🙂
Thank you, mam
you’re Welcome, Pawan!
God richly bless you for the kind and good work you always do for the good learners and freshers out there. Moreover, we the workers and employees at work also benefit more of your work teaches and practice.
May the good Lord continues His abundant blessings upon your life DIPSLAB.COM and My great woman !!
Thank You for your piece.
Glad!
Very very useful information
Thank you, SUBRAMANYAM.
Thank You.
Glad!
Thank You
Welcome, Buddika.
Thanks for sharing
My pleasure. Milind!
Updated more questions.
Yup!
Tandai
Informative indeed
Thanks, Simon:)
You’re most welcome, William. And thanks for sharing this post in your network.
Totally 30 question is important. It help me for improving my knowledge. Thank you mam.
If have such types of question then please forward my email
E-mail-vishnusopankharat@gmail.com
Yeah sure!
Thanks for sharing your mail. soon I will start sending the newsletter with my articles.
Vishnu, kindly subscribe to my Newsletter, you will get an automatic update about my new tutorials through the mail.
Good questions.
Thank you!
Thank you for this 30 questions which help me for interview.
Please share such articles to my email
pradipmahajan71@gmail.com
Sure, Pradip. Soon I will start sending the newsletter with my articles.
Really informative
Thank-you
Glad, It’s my pleasure.
Thanks, madam for sharing the tips. Would you like to share it on my email(akeee2017@gmail.com)?
You’re most welcome, Alok! Kindly subscribe to my Newsletter, you will get an automatic update about my new tutorials through the mail.
Good Knowledge!!
Thanks, Muhammad.
Madam,
sometimes it is required to pause the program & remove the chips. Can we do?
Hi Arvind,
Can you please elaborate, what chip you are talking about?
Hello Madam,
This article is really very nice. But, I want to add something to question no. 6
among the popular PLCs’. Please add our Indian PLC Messung and another popular plc which is GE Fanuc.
Thanks.
Thank you very much, Asif for giving a piece of updated information.
Definitely, I will add these two PLC brands.
Very good tutorial.
Thanks,Ram 🙂
A great thanks, Madam
Nice blog ma’am. It has enlightened my dark memories of the past few years and gives good knowledge.
Apart from that, I would like you to enlightened my badminton practice also. 😉
Thank you, Amit Patel:)
Provide complete information about A/D and D/A conversion with hardware and module with include of scaling function in it. I have some doubt in it.
Thanks, Savan for suggesting the topic.
I have noted your point. Soon, I will share and update here.
I had gone through all questions and it sounds really good. Do you something on python? so please share that also.
Thanks, Nandlal for reaching out to this article.
Sure. Kindly check the Python tutorial.
Hopefully, it will be very helpful to you.