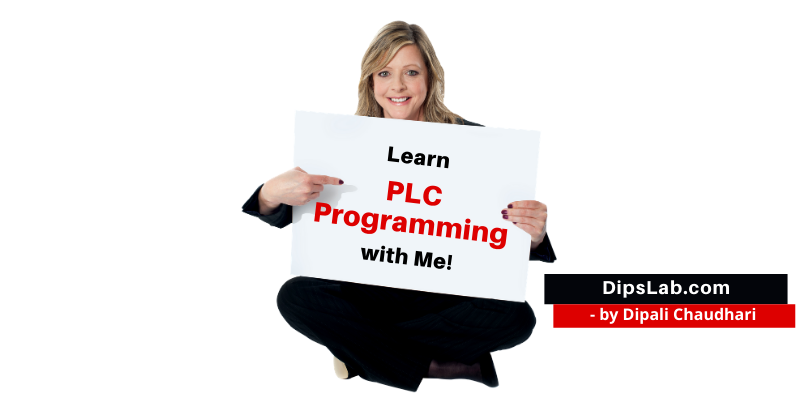
For industrial automation, the multiple programmable logic control (PLC) software, as well as hardware are used.
In an earlier tutorial, we have learned about multiple PLC software brands. Now, I am describing PLC hardware and its inbuilt PLC modules.
Different types of PLC Modules
What are the different types of modules used in PLC?
PLC hardware consists of different types of input and output modules in the form of analog and digital.
Different PLC brands design and manufactures different types of PLC hardware modules. Mainly, PLC hardwares are classified into three different types- compact, modular, and rack-mounted PLC.
Compact PLC:
Compact PLC type has inbuilt limited and fixed hardware modules. So, compact PLC is called as ‘fixed PLC’.
It contains only input, central processing unit (CPU), power supply (PS), output, and communicating modules.
Modular PLC:
Modular PLC type allows expansions of the PLC system through the use of additional modules.
We can add or connect the multiple modules in the hardware of the modular PLC. These several components are fitted on chassis or rack or bus with different slots.
Thus, the modular PLC is called as the ‘Rack-mounted PLC’.
For more detail you can read the difference between Compact PLC and Modular PLC.
AB and Siemens are the most widely used PLC brands. Let’s see, the description of hardware of modular or rack-mounted PLC modules which are used in AB PLC and Siemens PLC.
Here is the block diagram of the hardware of modular PLC where different modules are connected.
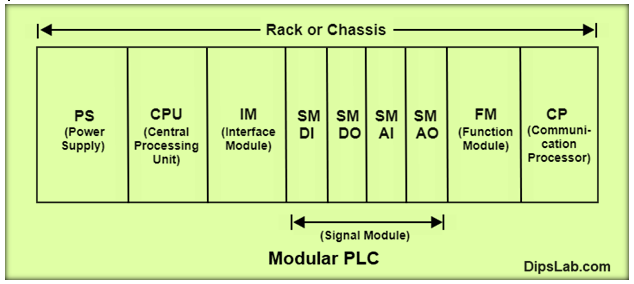
Explanation of each module one by one,
1. Rack or Chassis
The rack or chassis is the most important part of the modular or rack-mounted PLC system.
PLC rack or chassis is a hardware assembly that plugs every communicating modules together (like input, output, CPU, power supply, communication, and additional function modules) in a single frame.
In general, rack or chassis acts as a backbone of PLC system.
Read more: What is difference between PLC Rack and Chassis?
2. Power Supply (PS) Module
Power supply modules provide the required level of regulating power supply to connected modules in the rack.
This module is responsible for providing AC or DC power sources to operate the PLC through the backplane bus.
Typically, most of the PLCs work at 120V- 240V AC or 5V- 24V DC and backplane output current 2A to 5A at 5V DC.
3. Central Processing Unit
Central Processing Unit (CPU) acts as the brain of PLC system.
Basically, CPU performs arithmetic, logic, controlling operations specified by the programming instructions.
When we talk about PLC system, CPU has different type of operating modes.
- In programming mode, CPU downloads the logic from PC for an editing programs.
- In running mode, CPU executes the program for the process.
It is classified into the three important subpart like processor, memory, power supply.
4. Interface Module (IM)
The interface module is optional or an additional module.
It is used for the rack to rack communication in multi-tier configuration in modular PLC system.
5. Signal Module (SM)
Signal module exchanges the data information through the input and output modules.
- Input signal modules are used for connecting digital or analog field inputs to PLC.
- Output signal modules are used for connecting digital or analog field outputs from PLC.
These digital or analog I/O signal can be interfaced with through signal module.
6. Function Modules (FM)
The function module is also added as an optional module. It is used in only in modular PLC or rack-mounted PLC and not in compact PLC.
For the function module, you can use the analog and digital types of modules.
The high-speed counter modules, PID, weighing modules can easily connect to function modules. And PID, CNC, position controller can interface to PLC through function module cards.
7. Communication Processor (CP)
The communication processor is an optional module. It can be used for providing an additional communication port for communication protocols.
It is used for the networking communication between multiple processors or PLC. Also, CP exchanges data between PLC, SCADA, HMI, and other systems.
These are the 7 types of PLC modules that are mostly used in modular or rack-mounted PLC. These modules are required for communicating and data exchanging through the input or output signal.
If you are interested to learn PLC programming, read here step to step procedure for learning PLC programming and simulation.
If you are ready for online test, click on is a PLC Automation Quiz.
If you have any quires or difficulties, you can write in comment section.
Happy PLC Learning!
More informative.
Thanks, Ankit 🙂
Thanks, Dipali for sharing this infromation.
Glad, you’ve enjoyed it.
Excellent, I like it.
Thanks, John for reaching out to my blog. 🙂
Good, Mam.
Thanks, Rani 🙂
GOOD explanation.
Thank you 🙂
Thanks Ankit
very informative
Thanks so much for the blog article. Really looking forward to read more.
I’m really glad to see your comment, Shakil. Sure, I will try to share the more fruitful blog to the DipsLab readers.
Thanks madam
You’re welcome 🙂
Great post! I found the breakdown of the different Siemens PLC modules really helpful, especially the section on the benefits of each type.
Thanks, Thomas for your kind words!