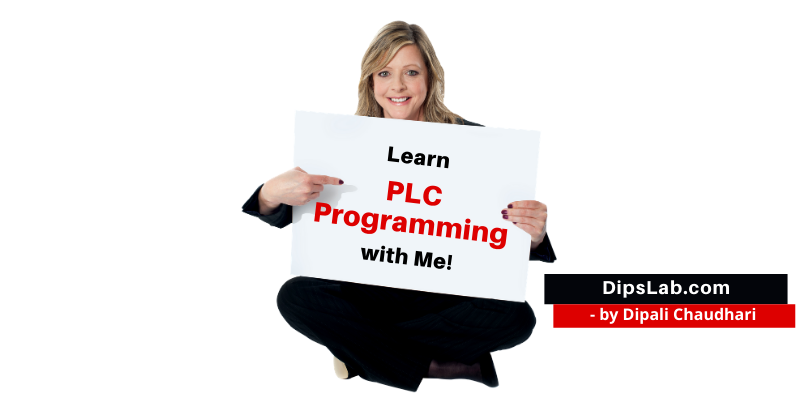
Today, we are studying the most used Programmable Logic Controller (PLC) communication protocols in the industry.
This article contains the top 31 communication protocols for PLC in detail.
Firstly, you should know…
What is Communication Protocol?
We all know the typical definition of communication protocol.
The communication protocol is a set of rules that govern data communication.
In other words, the communication protocol acts as an agreement between two or more communicating devices.
By using the communication protocols, two devices connect and communicate with each other.
Without communication protocol, devices can only be connected but not communicated.
List of PLC Communication Protocols
What are networking protocols used in Industrial Automation?
Here, I am listing the different types of communication protocols used for the automation of processes in PLC.
- EtherNet/IP
- Profibus
- Modbus
- Interbus
- ProfiNet
- ControlNet
- DeviceNet
- DirectNet
- CompoNet
- RAPIENet
- EtherCAT
- MelsecNet
- Optomux
- DF-1 Protocol
- HostLink Protocol
- MECHATROLINK
- DH- Data Highway
- PPI- Point to Point
- EtherNet Powerlink
- MPI- Multi-Point Interface
- EGD- Ethernet Global Data
- AS-i- Actuator Sensor Interface
- OSGP- Open Smart Grid Protocol
- DNP3- Distributed Network Protocol
- SDS- Smart Distributed System Protocol
- PieP- Process Image Exchange Protocol
- SRTP- Service Request Transport Protocol
- BSAP- Bristol Standard Asynchronous Protocol
- FINS- Factory Interface Network Service Protocol
- HART- Highway Addressable Remote Transducer Protocol
- Recommended Standard (RS-232, RS- 422, and RS-485) Protocols
These are the foremost communication protocols used for the PLC and other network connections. These protocols are supported by different PLC software brands.
The communication protocols are dependent upon three fundamental parts such as baud rate, network length, and the number of nodes.
More communication protocols are available in the market. You can easily buy PLC communication protocols.
What is the Baud Rate?
Baud rate is also known as Communication speed.
The rate of data transmission on the network is called Baud Rate. The unit of Baud Rate is bits/second (b/s).
In simple terms, it is calculated as the “number of data transferred per second”.
Characteristics of PLC Communication Protocols in Table
When PLC modules are connected over the network, standard communication protocols are used.
The different types of standard communication protocols support different speeds (baud rate), distances (network length), and the number of connecting devices (nodes).
# | Protocol/Cable | Baud Rate | Length | Node |
01 | Ethernet | 100 Mb/s | (Few Km) | 255 |
02 | Profibus | 5-12 Mb/s | 15 Km | 127 |
03 | MPI | 19.2- 38.4 Kb/s | 50 m | 32 |
04 | PPI | 187.5 Kb/s | 500 m | 1 |
05 | DH | 230.4 Kb/s | 3.048 Km | 64 |
06 | Control Net | 5 Mb/s | 30 Km | |
07 | Device Net | 500 Kb/s | 0.487 | 64 |
08 | USB Adapter | 57.6 Kb/s | 10 m | 1 |
09 | PC Adapter | 9600 Kb/s | 15 m | 1 |
10 | RS-232 | 19.2 Kb/s | 10 m | 1 |
11 | RS-485 | 10 Kb/s | 1.2 Km | 32 |
Which PLC communication protocol you should use?
- If you want to communicate with the more number of nodes with more speed, Ethernet is the best choice. You can read detail about ethernet here.
- If your network has a length of more than 25 Kilo-meter, you should use the Control Net protocol.
Binary Data Type Conversion for Baud Rate
Binary system based on the bit. Bit is either 0 or 1.
- 1 Nibble= 4 Bits
- 1 Byte= 8 Bits
- 1 Word= 2 Bytes = 16 Bits
- 1 Double Word= 4 Bytes= 32 Bits
Let’s see, binary data representation diagram.
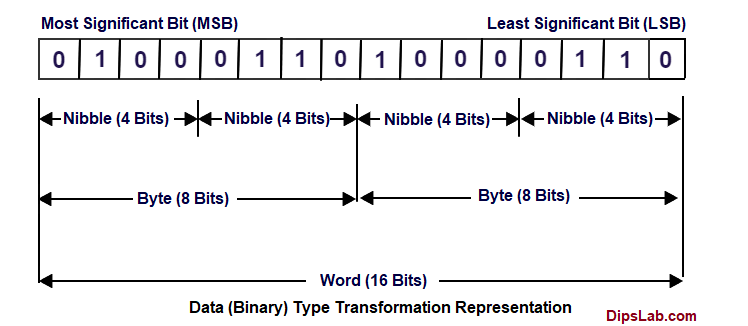
This is all about topmost PLC communication protocols. And I also covered the basic fundamental parts of protocol like Baud rate (communication speed), network length, and the number of nodes supported by each protocol.
Which communication protocol do you use for PLC? Share with me by commenting below. If you have any queries, let’s discuss them.
Other Related PLC Tutorials:
Happy PLC Learning!
Thank you….
Your welcome, Omprakash!
Good information and I want know about nodes. Can you make it?
Thanks, Bhagyaraju.
Kindly, elaborate on it. It will be helpful to me for making the node.
Thanks for the valuable info.
.We are using ethernet cat5 utp cable for controller communications to remote control room.
Your welcome, Ashar!
And Thank you for giving the information about the Ethernet protocol.
Thanks for the valuable information at one block useful to know more
Yup, Jahnavi.
Thanks for valuable information
You’re welcome!
Thanks for valuable information.
you can send me some PLC questions based on timer,counter,holding ,and project based ?
Thanks. I have noted your points. I will be listing all these questions in my upcoming tutorials with detail answers.
Good Job!
Thanks, Praful Patel
It’s a great work madam.
Thanks, Vishal!
Thanks, Vishal 🙂
Thanks a lot
Was really helpful and easy to understand.
You are most welcome, Rushab! and Thank you for appreciation
Very insightful
Thanks, Kapoko.
Please explain me that how can we select a servo motor and its drive in a machine and what are the parameters need to configure to run a servo motor with a drive .
Thank you…
Welcome, Soham!
Thank you for your valuable information. Please explain to me, what is the term ‘physical medium’ using in PLC Communication? I have some doubt about the same.
Hi Nishida. It is physical Media, not a physical medium.
In the PLC communication system, we are using physical media to transfer the data information from one place to another and as well for storing data. For these communication data storing and transferring, physical media refer to the physical materials in the form of conducting material.
There are three different types of Physical media used in a communication system – 1. Copper wire, 2. Optical fiber and 3. Coaxial cable.
If you have any queries or doubts, you can freely ask me.
Thank you so much Dipali..
Thanks a lot, Madam
You are most welcome.
Nicely Explained!
Please, explain how to link or communicate PLC with PLC?
Which kinds of communication protocols are commonly used and how to address multiple PLCs.
Thanks, Ahsan. Surely, I will try to soon publish the tutorial base on the PLC communication protocol in detail.
Thank you for your valuable information but I have still doubt in “nodes”? Can you please explain to me with a brief.
Yeah definitely, Akhil I will explain in an upcoming tutorial.
Useful information.Thank you very much.
You are most welcome!
Hi, thank you very much for your help, I Want to know what are the references for this table of characteristics of communication protocols.
Soon, I will describe in details and update this article.
Nicely explained!
To understand the Communication protocol your given table is very very useful.
Thanks a lot for the Characteristic table.
Thanks, Sandip.
Nice Information and well explained about communication protocol
Thank you very much. 🙂
Should include more info on basics like rs232, rs485.
Sure. I will write an individual article on different protocols.
Thanks, for sharing.
Glad, Mayank 🙂
It’s my first day to visit your website, Mam. Really, your articles are truly fruitful and helpful.
Thanks, Minal for reaching out to my portal.
Very useful information for me and easy to understand your writing content. Thank you very much.
Thanks, you too, for your kind word.
Thanks a lot mam
You’re welcome, Sushil:)
RS485 is not a communication protocol, it is a bus specification.
RS485 is a communication protocol which can be designed for bus communication.